The Risks Associated With Abrasive Wheels
Abrasive wheels are widely used for manufacturing purposes. They can perform grinding, cutting and drilling tasks, and they are an integral part of equipment such as chop saws and surface grinders.
However, there are significant risks associated with using abrasive wheels. It is essential for both the health of the operative and the reputation of the business that these are properly controlled and the appropriate abrasive wheel training is provided.
What Are The Main Risks
There are many potential hazards surrounding the use of abrasive wheels. However, the ones relevant to your situation will be dependent on the type of equipment that you’re operating, your working environment and the material you’re working with.
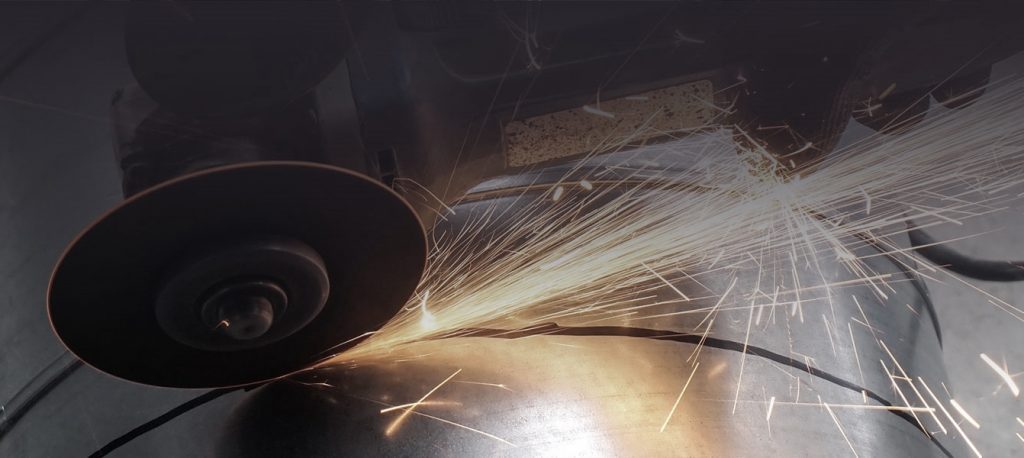
Touching the Wheel
An accidental touch of the wheel can cause the operator serious damage, and this is down to the power of the machine. Tools which are designed to cut and grind will cause significant damage if they come into contact with human skin.
This is a key example of why personal protective equipment is essential, and why operators must be required to wear the appropriate gear. Learning techniques from a competent instructor can also reduce the potential for injury.
Bursting Abrasive Wheels
A bursting wheel has the potential to be fatal for the operative or anyone within its vicinity. This is a particular risk with new wheels, and it can be controlled with practices such as ensuring the wheels are run within the suggested speed parameters and providing the appropriate guarding.
Additionally, appropriate abrasive wheel training must be provided (this is a legal requirement). This will help staff learn the correct procedures involved, such as handling and mounting the wheels.
Sparks
When in use, abrasive wheels can create sparks. This has the potential to lead to fires or even explosions if their surroundings aren’t keep clean and ventilated.
In order to protect against this, it is the duty of both the employer and those using the wheels to ensure clean, well-ventilated working environment. Personal protective equipment (PPE) such as gloves and eye protection should also be worn, and any guarding should be in place.
Reduced Blood Circulation
The vibrations associated with abrasive wheel operation can occur when the incorrect type, size or weight of wheel is used with the machinery. Loose bearings are also a possible cause of this, as well as a faulty wheel design.
All of this can cause discomfort and in some circumstances, it can also result in a condition known as hand-arm vibration syndrome (HAVS).
“HAVS is a painful and disabling condition that affects the nerves, blood vessels, muscles and joints of the hands and arms. It causes tingling and numbness in the fingers, reduces grip strength and the sense of touch, and affects the blood circulation” (HSE)
To avoid this, it is important that the correct wheel type is chosen. If the operator is beginning to feel discomfort or tingling as a result of their job task, they should report this to management immediately.
Dust and Gas Inhalation
Although this does depend on the material in question, dust and gas inhalation can affect the health of the operator and cause serious consequences to their health.
Because of this, it is important to manage the environment they’re working in, again ensuring that it is well ventilated. The operative must also wear the RPE for the task at hand.
Participate In Our Abrasive Wheel Training Courses
Whether you have a large team or a singular person that requires training, we can help you to protect your workers and comply with regulations. We offer a variety of courses to cater for different requirements.
If you would like to learn more about any of abrasive wheel courses, please get in touch today.